March 19th, 2024
Despite the numerous advantages that come with injection molding including high production efficiency and cost-effectiveness, there are inherent risks associated with it as well. Regardless of the final product, there’s always the possibility that something could go wrong, requiring thorough control techniques to mitigate any uncertainties.
Risk management in the injection molding industry is not merely a regulatory requirement but an essential business strategy. The multifaceted nature of the industry’s risks – ranging from operational disruptions and financial volatilities to safety hazards and environmental impacts – demands a comprehensive approach to management. By identifying, assessing and proactively addressing these exposures, companies can achieve several critical objectives such as:
- Enhance Operational Efficiency: Mitigation strategies associated with equipment failure, supply chain disruptions and production inefficiencies help ensure smooth operations and reduce costly downtime.
- Ensure Product Quality and Compliance: Managing concerns related to product defects and non-compliance with industry standards is vital for maintaining customer trust and avoiding legal liabilities.
- Protect Worker Safety: Hazardous incidents in the workplace can lead to personal injuries or worse. A robust deterrent framework helps create a safer working condition, reducing the likelihood of accidents.
- Helping the Environment: Addressing harmful environmental issues by minimizing waste and promoting sustainable practices is increasingly important for regulatory compliance and corporate responsibility.
- Financial Stability: Budgetary problems, including fluctuating raw material costs and investment in technology, can be managed through planning and modification programs that promote confidence in the company’s fiscal wellbeing.
To achieve these objectives, the injection molding industry employs various procedures, both internally and externally. While this may vary among companies, the key tactics include:
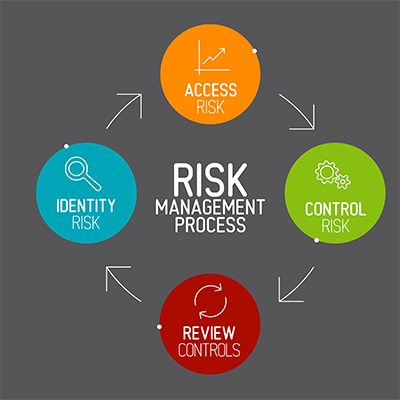
1. Risk Assessment and Analysis
The first step in dealing with risks is identifying potential hazards within the operation, from the procurement of raw materials to the delivery of finished products. Conducting regular assessments and utilizing tools like SWOT (Strengths, Weaknesses, Opportunities, Threats) analysis or Failure Mode and Effects Analysis (FMEA) can help organizations anticipate and prepare for potential challenges.
2. Process Optimization and Control
Implementing strict limits and continuously checking parameters solidifies consistency and high quality in a manufacturing setting. Methodologies such as Statistical Process Control and Total Quality Management can be invaluable in detecting and correcting deviations and contribute to peak performance.
3. Advanced Equipment Maintenance
Preventive and predictive maintenance schedules for injection molding machines and auxiliary apparatus lessen the chance of unexpected breakdowns and prolong equipment life. “Smart” innovations like Internet of Things sensors can predict failures before they occur, allowing for timely interventions.
4. Employee Training and Safety Programs
Comprehensive training programs for employees on the proper use of machinery, safety parameters and emergency response can significantly minimize workplace mishaps. Encouraging a culture of safety and making personal protective equipment (PPE) readily available are also key components of a successful approach.
5. Supply Chain Management
Diversifying suppliers and developing strong relationships with them can limit potential difficulties connected with raw material shortages or delays. Just-in-time inventory strategies and supply chain visibility tools can also help manage inventory levels efficiently and reduce the likelihood of production halts.
6. Financial Risk Management
Financial risks can be avoided through careful budgeting, forecasting and the methodical allocation of resources. Hedging tactics may also be employed to shield against raw material price volatility. Adequate insurance coverage on equipment, liability and business interruptions is essential for protection to counter unforeseen events.
7. Environmental Management Systems
Implementing an Environmental Management System (EMS) compliant with international regulations like ISO 14001 can help curb environmental threats. This includes initiatives to lower waste, recycle and use energy competently, with the intended result being to diminish the ecological footprint of manufacturing operations.
8. Regulatory Compliance and Continuous Improvement
Staying abreast of and complying with industry code and protocols is crucial to avoid legal and financial penalties. Adopting a mindset of continuous improvement through methodologies like Lean Manufacturing and Six Sigma can drive efficiency, reduce waste and optimize risk management efforts.
Risk management is a critical – yet often overlooked – aspect of the plastic injection molding industry. Its importance cannot be overstated, and processes are continually adapted to best serve current revolving business situations. Embracing robust risk routines will lead to improved outcomes, valuable results and lay the foundation for long-term success and resilience in the face of uncertainties. This kind of calculated application guarantees that the plastic injection molding industry remains adaptable, competitive and ecologically sound in an ever-changing business landscape.
The Slide Products team of factory experts, in conjunction with its distributor network, are available to guide customers with proper procedures and maintenance techniques through our Top Tier Service program.