February 4th, 2025
The aerosol spray is one of the most fundamentally altering products of the 20th century, influencing how things are packaged, stored and dispensed today. From consumer use to military utilization, this innovation has played a pivotal role in technology advancements, environmental challenges and industrial trends.
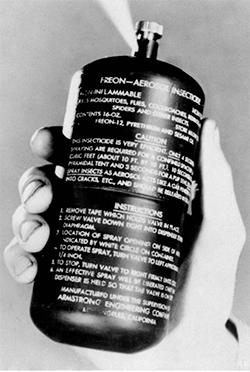
The First Aerosol Spray Can – 1927
While the concept of an aerosol originated as early as 1790, the invaluable tool was patented by Erik Rotheim, a Norwegian engineer and inventor, on November 23, 1927. During this period, he specialized as an electrochemist and found a revolutionary way to perfect a propellant system that could hold and subsequently distribute desired content from its metal can (base) through an attached valve apparatus.
Rotheim realized that when colorless gases of Chloride Monomer (VCM) or Dimethyl Ether (DME) are used, a chemical reaction occurred that created the catalyst to get the formula out of a can. His ingenuity was inspired by a methodology to spray compounds for coatings used in soaps, resins, paints and other substances that could be nebulized.
Birth of Propellants – 1930
While Rotheim tailored his devices to be more efficient, fellow chemical engineers Thomas Midgley and Charles Kettering were developing a new refrigerant gas.
Known as dichlorodifluoromethane, a low toxic prototype of chlorofluorocarbons, this gas was recruited as a main coolant fluid in compression refrigeration cycles. Effective and versatile, the synthetic product became one of the main propellants for aerosols.
DDT: First Spray Pesticide – 1942
War demands called for an increase on portable insecticides. Over 30 million cans were supplied to the U.S. Army and Air Force. Lyle Goodhue and William Sullivan created a small, pressurized type powered by liquefied gas (fluorocarbon). This breakthrough instigated the production of hair sprays. Supplementary to this inventiveness, in 1949 Robert Abplanalp went on to create and perfect the crimp-on valve, a revolutionary reliable part that would spur the creation of countless new products.
Post-War Consumer Adoption – 1950s-60s
In 1953, Abplanalp’s patent was official on the crimp valve "for dispensing gases under pressure." He started the Precision Valve Corporation and soon was earning over $100 million dollars producing one billion aerosol cans in the USA and one-half billion in several other countries.
By the 1950s, shaving cream, room fresheners and cleaning products transitioned to these upgraded containers. Having the ability to store products under pressure and use them in a controlled mist easily and proficiently accelerated a growing popularity among consumers.
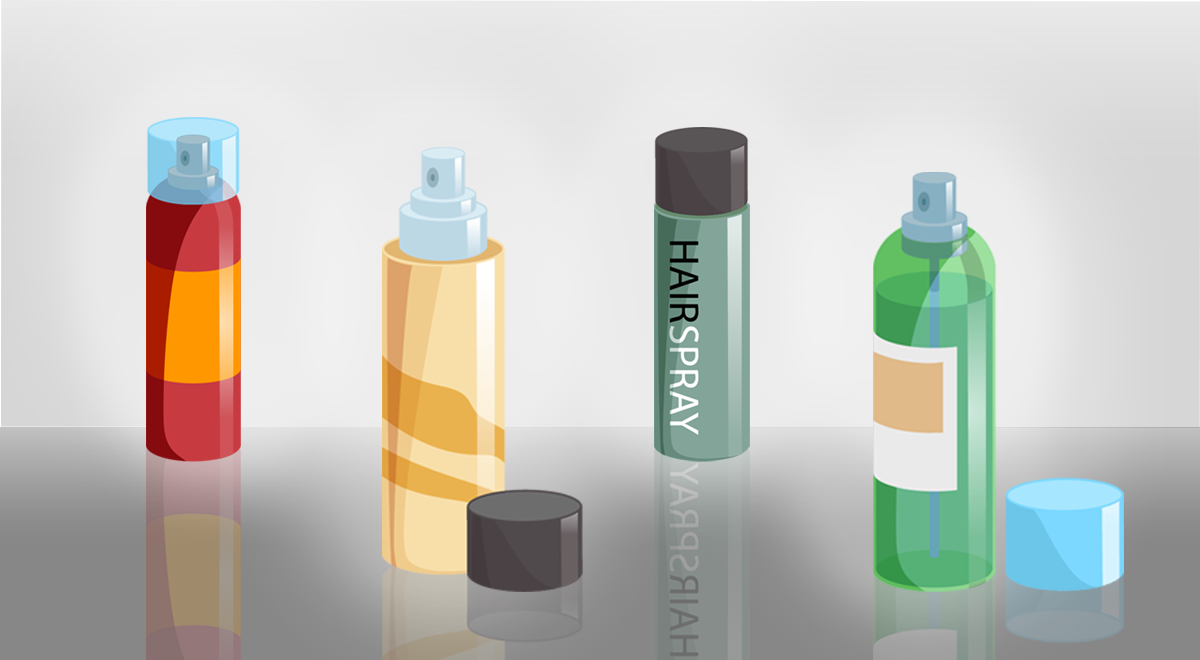
CFCs: Refinement – 1970s-80s
At this point, production of aerosol cans had increased by over 80%. In the 1970s, environmental concerns arose due to a report by Molina/Rowland who targeted aerosols as a threat to the ozone layer. A chemical compound made up of chlorine, fluorine and carbon (CFCs) were thought to have contributed to this issue.
By mid-1970s, increasing trepidation over the use of CFCs sent Abplanalp back into the lab for an answer. Changing to water-soluble hydrocarbons rather than fluorocarbons made an eco-friendlier version. This catapulted aerosol products to a higher level.
Environmental Concerns – 1990s-2000s
Environmental protection ran the forefront of aerosol manufacturing in Europe, thought to be leading producers of these cans. The Montreal Protocol (1987), an international treaty, phased out the use of any other harmful chemicals for a transition to safer ingredients. They provided CFC-free labelling in 1989 and consumer aerosols have remained without such toxic formulations ever since.
Modern Innovation – 2000s-present
A new wave of pioneering technology effected product design to become more ecologically compatible. The initiative of producing greener propellants and materials triggered hydrofluoroolefins (HFOs) to replace older methods. The cans themselves became lighter with options for valve mechanisms to propel consistent spray patterns.
For the foreseeable future, we expect to see a focus on enhanced sustainability, recycled metals and biodegradable solutions.
Advantages of Slide Aerosol Products
- Ease of Use – Allow for mess-free applications with a simple spray onto a desired surface without the use of brushes or applicator.
- Precision – Adjustable attachments such as nozzles and extension tubes give users a direct path to the intended area.
- Clean Coating – No tools or gloves necessary; these products offer a consistent, even finish with ensured uniform distribution.
- Fast Drying – Many of Slide’s aerosols are formulated for a quick-dry application that gives long lasting lubrication without excessive buildup.
- Convenient – Compact portable nature makes them easy to transport and store, perfect for on-the-go maintenance or repairs.