May 20th, 2025
Injection molding is the ideal manufacturing solution for producing large quantities of parts efficiently and consistently. A critical factor in achieving high quality products is in the mold design selection, as the mold and material used has a direct impact on performance and durability.
When choosing a mold, it is important to not only acknowledge immediate production needs, but long-term reliability and economic stamina. This article will explore the two most popular mold materials – steel and aluminum – and compare their attributes to help you make an informed decision based on your production needs.
Tooling and Part Cost
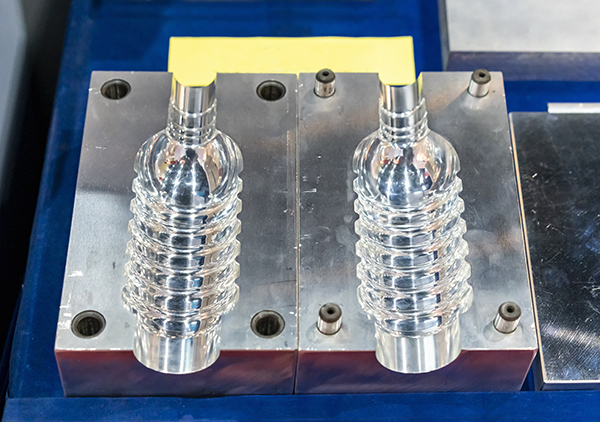
Where price is the initial factor, aluminum is significantly cheaper to produce, and therefore the better choice. Because of a lower upfront expense, this metal is more attractive for prototyping, pilot runs and low volumes. In addition, aluminum supports shorter processing times, adding to a lower overall cost per part.
Conversely, if dealing with larger loads, steel offers enhanced benefits because it can withstand bigger quotas and frequent maintenance stresses. At the outset a significant investment will be necessary. But since this alloy has a longer lasting lifespan it will help produce millions of vital products and generate solid economic advantages.
Advanced Materials
In applications involving complex formulations including reinforced fiber, glass and additives – steel affords a superior solution compared to aluminum. The strength of steel yields better resistance to chemical degradation and wear.
Aluminum is a softer element and can be subject to a copious degree of scratches and damage. This can affect the overall texture, appearance and performance of the outcome.
Thermal Properties
Heat conduction is critical in creating a uniform resin flow to fill a mold cavity across all distances.
Aluminum is almost five times more thermal conductive than steel; therefore, it provides faster heat dissipation. The heating and cooling process of aluminum results in a short succession cycle that’s especially useful for low quantity production.
Steel molds have a smaller thermal conductivity and slower heating/cooling ratio, which translates to extended cycle phases. While more difficult to machine, this special property helps facilitate the creation of complex components requiring tight tolerances.
Defects
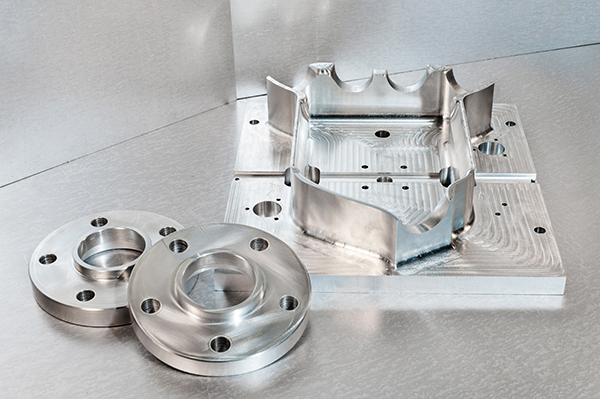
Faster heat dissipation in aluminum makes for even temperature fluctuations. This helps to limit the number of defects as unstable cooling can cause warping, burn marks, voids and sink marks.
Comparatively, steel is quite reliable for producing top quality items when utilizing proper design measures. However, gradual temperature vacillations can increase the likelihood of flaws.
Repair
Aluminum molds are easier to machine and modify due to their malleability. If design changes are called for or manufacturing issues arise, it provides flexibility and lower repair costs.
Steel, while much harder to deform, is more difficult to damage but expensive to repair if desecration does occur. Steel is resilient enough to reduce the frequency of such repairs in high volume productions.
Durability
The composition of steel furnishes superior fortitude, solidity and abrasion-resistance. This supports long-term, big bulk manufacturing for millions of rotations with minimal deterioration.
On the other hand, aluminum has a quick heat flow trigger leading to rapid expansion and contraction. This can mean dimensional instability (especially under pressure), creating a softer surface that is susceptible to wear down.
Detailing
Some applications call for tighter, narrow tolerances with intricate detailing and in these cases, steel is generally the dominant choice. The permanence, firmness precision and consistent quality make it perfect for complex components.
Alternatively, aluminum can achieve good exactness, but is prone to degrade quicker, bringing about decreased accuracy and drift over time.
Overview Comparison
Steel Molds
For complex, long-term processing
- Ideal for high scale fabrication, these molds are extremely durable and can handle up to millions of sequences.
- Although often costly to make, steel molds provide an excellent and reliable outcome.
- Regarding tolerances, steel offers an improved strict finish by maintaining an exact fit.
Aluminum Molds
For simple, low volume processing
- Suitable in fast processing settings, aluminum molds are compatible with low to mid-scale production.
- You can expect to see shortened cycle phases at a greater affordability over steel.
- Softer in stature, you risk compromised precision after prolonged usage.