January 23rd, 2024
As we reflect on the past year, there is no doubt that 2023 brought many significant advancements within the injection molding industry. With developments reflecting ongoing technological growth, environmental concerns and fluctuating market demands, manufacturers continued to adapt to the new “normal”.
Slide was once again challenged to consistently provide the best results to our customers despite ever-changing circumstances. New products and procedures were created with our high-quality standards in mind, and a commitment to ultimately reduce cycle times. As we look back on 2023, here are five of the most notable trends and where we expect to go in 2024.
Advanced Automation and AI Integration
Automation in the plastic injection molding industry reached new heights this year with the integration of Artificial Intelligence (AI). Factories, equipped with AI-driven machines, can optimize production, reduce waste and improve quality control. These machines are capable of self-monitoring and adjust in real-time to maintain ideal operating conditions. This technology is not only improving efficiency but also transforming the workforce, requiring new skill sets for machine operators and technicians.
Moving forward, there is no doubt that AI will continue to take the front seat in technological advancements. Such proficiencies will play a crucial role in predictive maintenance, quality control and process optimization, among others. However, with so many unknowns and variables, it could be a slow rollout.
Sustainability and Eco-friendly Materials
Another trend that was prominent in 2023 was a larger shift toward sustainability. There was an increasing demand for eco-friendly materials in injection molding, such as bioplastics, repurposed plastics, and related procedures successfully utilized. Additionally, environmental regulations became stricter, impacting the ways in which the industry operates as a whole. Manufacturers are now more accountable for consciously reducing harmful emissions, managing waste and ensuring their products are recyclable.
As a movement that has been prominent for decades, we expect the focus on conservationism to continue in the fight against climate change. Specifically, the adoption of all-electric injection molding machines is projected to ramp up and offer energy savings over traditional hydraulic-based equipment. With new methods being discovered to reduce our global footprint, low-waste and emission initiatives are becoming more and more crucial to manufacturing companies.
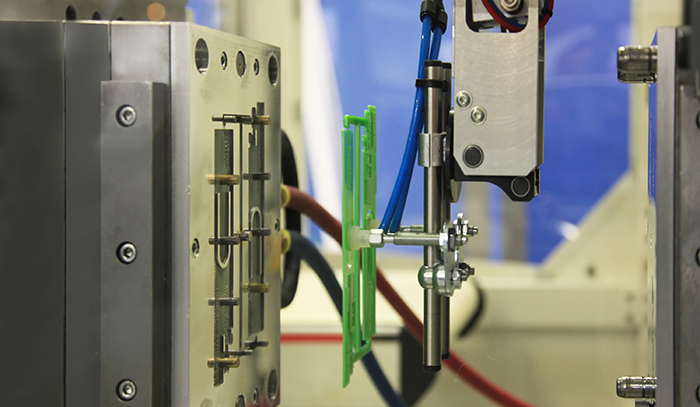
Customized and On-Demand Designs
Developments in molding technologies brought about an upsurge in the production of complex parts at increasingly tight timelines. The ability to produce intricate designs with high precision and small
quantities has opened fresh possibilities in various sectors such as healthcare, automotive and aerospace. This practice is particularly important in medical applications where patient-specific implants and devices are becoming commonplace.
We see a tendency towards pinpointing identifiable purposes as on-demand applications are discovered. Since this has the potential to affect many different industries, it will become standard as a familiar injection molding model. Additionally, it would ultimately prove more cost-effective for lower production volumes.
Increased Use of High-Performance Polymers
High-performance polymers, known for their superior strength, temperature resistance and durability, realized magnified consumption in 2023. Plastics are particularly vital in industries like aerospace and automotive, where rigorous components are required. The greater use of polymers is in response to the growing need for materials that can withstand harsher conditions along with added durability.
Large investments are being put into superior-performance polymer research which will translate to additional treatments across numerous industries. Though currently representing only 1% of total plastics utilization, materials are needed at a rate faster than the market can bear.
Shorter Supply Chains
As an effect of pandemic-invoked supply chain disruption, many companies have chosen to localize their processes including injection molding and tooling manufacturing. This measure includes several benefits such as enhanced product quality, reduced transportation costs, decreased lead times and boosted sustainability.
While centralized production has been gaining attention throughout the last couple of years, economic indicators confirm that plastic manufacturer relocation significantly slowed down in Q4 of 2023. Therefore, we estimate that a downward slide will continue despite any potential 2024 improvements. Check out our related article to learn more about this topic.
In conclusion, the trends of 2023 plastic injection molding highlight a segment that is rapidly evolving, driven by technological innovation and a growing awareness of environmental and social responsibilities. These inclinations are not only shaping the present landscape but are also setting the stage for future expansions. As we look ahead, it's clear that our industry will generate challenges, but also be ready to eagerly meet contemporary prospects for growth and improvement.
From all of us at Slide, thank you for another great year and we look forward to a successful 2024!