August 22nd, 2023
The tactile quality of pulling a new record out of its sleeve can’t be replaced with the digital music of today and may explain why vinyl is making a comeback. That’s good news for Chicago’s very own Smashed Plastic who provides a full suite of services to get projects pressed onto vinyl. Located in the heart of downtown Chicago, they are getting records into the hands of fans everywhere. SP recently reached out for some purging assistance from Slide’s Michael Muth and Jeff Lewis, who were anxious to help.

As with other plastics processing, a variety of colors is often used to make records and artists have been getting more creative with their production requests. Smashed Plastic thus faces the same issues as other plastics mold manufacturers do when purging. Dark color residue inevitably remains in the system and is difficult to flush out, resulting in streaking, specking and a high scrap rate. Due to the delicate nature of records and etching songs onto them, these final products cannot be created by any re-grind method.
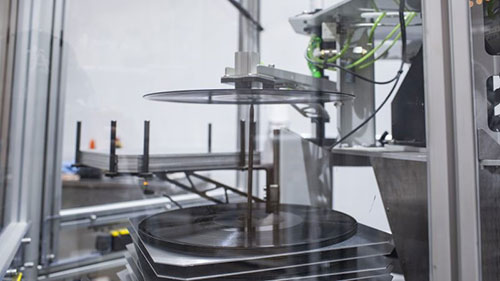
Record Making Process
- Once the music has been recorded, edited and mixed, the arduous record making procedure can begin.
- The lacquer phase consists of cutting grooves into a nitrocellulose coated aluminum plate – one is cut for each face.
- A master disc is formed by spraying the lacquers with a solution of silver submerging it into a nickel electroplated bath.
- This causes the nickel to bond with the silver particles and produces the grooves on the surface.
- The resulting master will be pulled apart into two separate parts that are mirrors of each other – the original has grooves and the other has ridges.
- The latter is referred to as the “father” and what will be used as a stamper for pressing records.
- The next step is to check for any errors on the exterior, but because it has ridges it must be electroplated and split once more to form what is called the “mother” and the final stamper used to press the vinyl completed copy.·

To press the new vinyl discs, polyvinyl chloride (PVC) pellets are poured into a hopper which will extrude the material into a “biscuit” or small puck shape. These biscuits are placed on top of the label and then pressed at high temperatures into a record mold, with any excess getting trimmed off. Now they are ready for sleeve placement and sent off for music fans to enjoy!
Solving Specific Problems
Smashed Plastic tried Slide’s KLENZ Purging Compound and had previously used PDQ Liquid Purging Compound, but thought the process with PDQ was a little messy since it’s a wet purge. Jeff suggested a procedural change for which they were previously unaware. He also left samples of Econo-Purge to aid in dislodging any really tough pigment that might get stuck in the barrel.
The record manufacturing industry has grown up using a re-grind method for purging. The technique entails chopping up damaged vinyl into very small pieces and recycling it back into production. During this stage, undesired colors should be expelled resulting in a clear polymer. The record making process can begin again with transparent plastic and run through the color spectrum until reaching black, when it will be necessary to purge again to return to lighter colors. At this assembly point, Slide recommends adding their Econo-Purge formula. Taking some time out to do so should help keep machinery clean if a step of soaking and clearing the nozzle head is included.

Jeff noted, “It was wonderful to get out here and work with the Smashed Plastic crew. Covid played a role in delaying opportunities to visit on-site and review their productions methods. However, I’m confident the adjustments we’ve made to their routine will help increase processing speed and production.”
This was an especially interesting visit as Smashed Plastic is located in the same building where Hammond organs were once made. The original smoke stack is still present and the old steam boiler has been incorporated into their bar area. The building itself is now transformed into loft type spaces and the staff of about a dozen enjoys open workspaces.
Smashed Plastic is the biggest record producer in this region and is part of a small market niche. What they craft is truly an art form and can’t be accomplished by just anyone. It’s important for the company to be able to get back into fabrication quickly after these color changes. Being in a continual state of production is necessary for them to meet the demands of the artists, and especially for those “kickoff” events where small quantities of records are required for release parties.

Slide Is at Your Service
Our experts can easily be reached to assist you with your purging questions or concerns. You can receive complimentary assessments, advice and training through our Top Tier Service program. We also offer free trial samples of our products so you can try before you buy. Contact us directly, through your local distributor, or by phone at 1-800-323-6433.