December 19th, 2023
Automation has been revolutionizing various industries for years, and injection molding is no exception. Robotic systems and advanced software have made it easy to control and manage the molding process, enhancing efficiency and consistency along the way. Affecting everything from manufacturing operations to workforce dynamics, there is truly no limit to where this new technology will go.
Below we will explore the transformative impact of this innovative procedure on injection molding, highlighting the advancements, benefits, challenges and future implications of this transformative integration.
Advancements in Automation Technologies
One of the most notable improvements is the use of precision robotics. These mechanics are connected to equipment and can perform tasks like loading plastic pellets into machines, removing completed products and precisely cutting or finishing parts. Additionally, smart sensors and control configurations have been developed to monitor injection molding in real time, ensuring uniform quality and reducing waste. These automatons have been crucial in resolving manufacturer’s productivity concerns and commonly exceed their expected return.
Benefits in Injection Molding
There have been many significant benefits that wouldn’t have been possible without this exciting breakthrough. By filling in where humans cannot, we’ve witnessed remarkable changes in the past couple of years including:
Enhanced Efficiency and Production
These systems can operate continuously without fatigue, leading to significant increases in production rates. This enhanced capability also means faster completion times for projects, which is vital in a market that demands rapid turnaround.
Cost Reduction
While the initial investment in programmed technology can be substantial, it eventually generates savings. Computerized procedures utilize supplies more effectively, reduce labor overhead and minimize spoilage throughout entire functions.
Improved Quality and Reliability
Reducing human error, automation leads to a higher consistency in product quality. The precision of robots and control systems guarantees that every part is made to the strict specifications required, time after time.
Scalability
As demand fluctuates, this process allows for the easy scaling of operations. Businesses can increase or decrease production without the constraints of hiring or laying off workers, providing a stable fabrication mode that can adapt to market needs.
Better Use of Human Resources
With automation taking over repetitive and mundane tasks, the human workforce can be redirected to more complex and creative matters such as design, programming of machines and maintenance. This converts to added job satisfaction and growth of a skilled workforce.
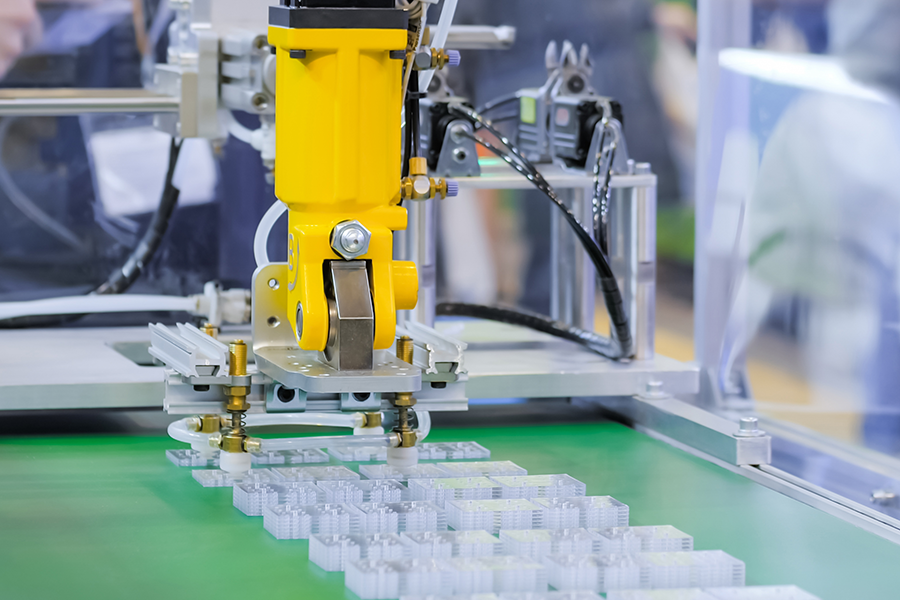
Challenges and Considerations
Along with any new mechanization, there are also downsides. Most prominently, the expense of implementing these systems can be a barrier for smaller manufacturers. It often requires advanced equipment and training to keep up with an ever-changing technology. Additionally, a workforce of this caliber and knowledge is a challenge to sustain. Even so, the long-term savings and increased yields frequently justify the spending.
Future Implications
Moving forward, this production method is expected to become more integral in the injection molding industry. With evolutions in artificial intelligence (AI) and machine learning, these networks will become more adaptive and robust. It could lead to even greater performance and the ability to produce other complex parts with minimal human intervention.
Furthermore, as sustainability becomes a larger concern, robotization can play a crucial role in developing more environmentally friendly manufacturing applications. Automated systems can optimize the use of materials and energy, thereby easing the environmental footprint of the injection molding process.
Robotics is in the lead of innovations that are expected to dramatically alter the landscape of injection molding. Slide Products continues to monitor this cutting-edge advancement. The benefits to both producers and consumers alike are undeniable. There’s no doubt that the industry constantly evolves, and we’re eager to see what resources such remarkable developments will hold for the future.