May 6th, 2025
Despite its efficiency and widespread use, injection molding entails several safety perils that are essential for which operators and supervisors need to be cognizant. This process involves flammable materials, hot surfaces, molten plastic and moving parts – all of which pose potential risks.
To mitigate the likelihood of burns, shocks, hearing damage, eye and other injuries, workers should have appropriate gear and receive training in strict safety protocols. The following key measures are meant to maintain a secure and compliant manufacturing environment.
Training Practices
Providing personnel with comprehensive knowledge and best practice techniques before executing any task allows each job to get done safely and proficiently. It is not only important to recognize the dangers but also take proactive steps to avoid them. Employees need to become familiar about the entire method, resources and machinery involved.
- Initial instruction, in addition to demonstrations covering procedures, control systems and machine mechanics must be incorporated as a standard preparation to streamline careful production.
- Inform operators about emergency response situations, such as explosions or fires, and have access to detailed shutdown plans.
- When new updates arise or requirements change procedurally, express them immediately.
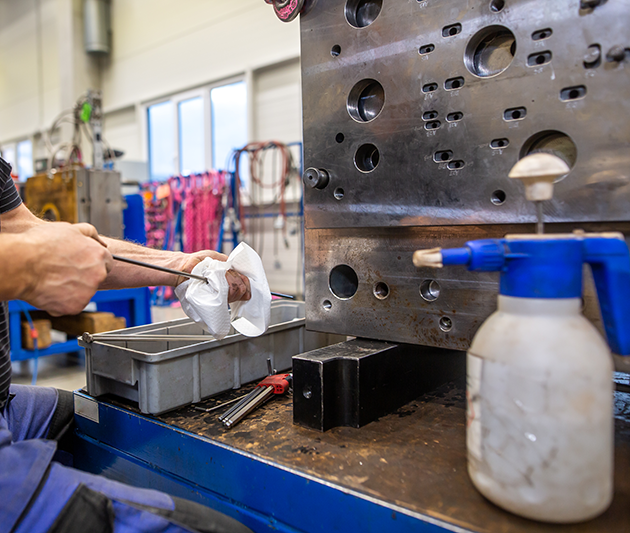
Regular Maintenance
Routine inspections and preventative maintenance, encompass checking for signs of damage or wear on machines (which can lead to malfunctions or accidents), are crucial for keeping a sound work environment. Injection molding equipment contains intricate parts that are essential to production and should be inspected before the operation cycle begins.
- Conduct a thorough assessment of machines at least every six months to prevent electrical issues in systems containing wiring and connections.
- Monitor temperature and pressure readings daily to identify deviations from a normal range.
- Perform regular mold and part servicing – including lubrication, cleaning and examination – to deter the possibility of larger problems developing.
Chemical Handling
Substances used in this method often involve various raw materials that may pose a threat to handlers/manufacturers. Adhering to appropriate measures is central to bypass dangerous incidents.
Safety Data Sheets
Certify that access to information regarding all chemicals utilized is made available on SDS. Annual reviews of SDS files should be completed to ensure the most up-to-date and accurate chemical and safety information is on hand and made available to employees.
Addressing Spill
Offer detailed instruction and have supplies readily accessible for cleanup and disposal of contaminants.
Proper Storage
Store materials using clear labeling related to their composition and follow OSHA storage guidelines thus reducing the chances of toxicity or undesirable reaction.
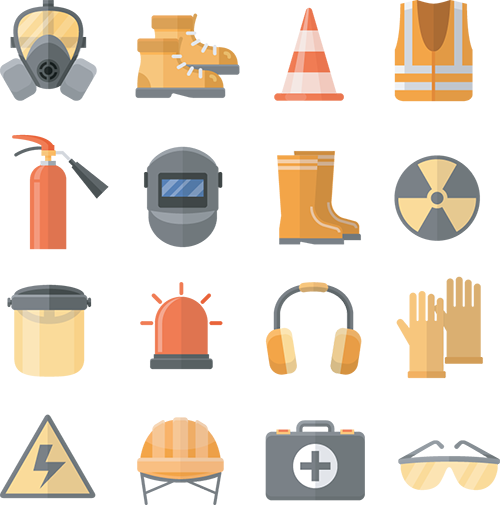
Personal Protective Equipment (PPE)
Understanding the protocols and standards aren’t enough – proper use of defensive gear is imperative to avoid injury, as the operation entails high temperatures, pressure changes and chemicals. Personal protective equipment (PPE) is required when operating as a necessary layer of defense. These guidelines must adhere to standards established by OSHA (Occupational Safety and Health Administration) and ANSI (American National Standards Institute).
Hearing Protection
Wear earplugs or earmuffs to avoid noise-induced hearing loss, as high decibels are often present during the injection molding process.
Protective Glasses
Utilize impact resistant, snug fitting anti-fog glasses to keep out debris, including excess waste from molten plastic.
Gloves
Choose puncture-resistant gloves made of heatproof fabric, such as leather or Kevlar, to defend against cuts, burns and other abrasions.
Steel Boots
Use ASTM F2413 standard compliant shoes made of non-slip, insulated leather for optimal armor against electrical shock, compression and impact.
Respirators
In cases of handling materials containing fine particles or fume emissions, use a ventilatory shield such as respirators or approved face masks.
Machine Guards
Always secure all equipment barriers in place beforehand to prevent workers from encountering moving parts.
Chemical Exposure
Ensure that proper ventilation, such as exhaust systems, is installed and operational when working near molten resins that emit harmful fumes.
When immersed in injection molding production, temperatures, pressure and high-speed machinery can pose a challenge, making precaution a top priority. By emphasizing safekeeping measures and implementing them regularly, you can minimize the chance of injuries such as burns, electrical shock, eye/ear damage, and affirm a safer workplace. Together, the combination of training, PPE and routine maintenance supports a productive and secure manufacturing environment.